Illawarra Smallgoods Project
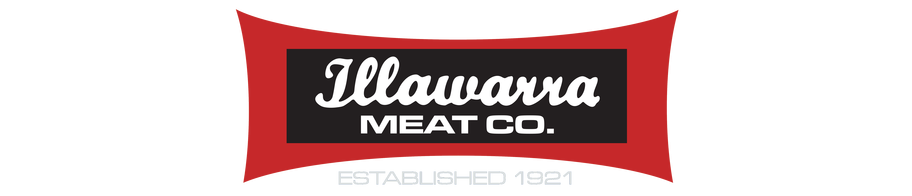
Client: Illawarra Smallgoods
Location: NSW
Meat producers, Illawarra Smallgoods in NSW required a high-density storage solution to house packaging materials. APC was selected for the job for identifying a high density storage solution that suited the client’s exact requirements.
Briefing
Illawarra Smallgoods produces sausages and other meat products which they supply to supermarkets, restaurants and wholesale outlets. They wanted to optimise the storage capacity of their packing material supply chain. They had used Drive-In Racking in past, however, due to various reasons they were looking for a long term and better value for money solution. APC was selected for the job for presenting a solution that suited the client’s requirements. Our solution was a Satellite Racking System: a semi-automated, deep lane pallet storage retrieval system, combining high - density storage with improved pallet and pick face access.
Challenge
With a storage space of just 420 square metres, the client required a high-density storage solution capable of holding 476 pallets. Another challenge was to provide levelled racking across unlevelled warehouse flooring with some areas experiencing up to 250mm variation in height.
Solution
With more than 45 years in the storage industry, APC identified the client would benefit most from Satellite Racking. The deep lane, semi-automated storage system does not require the forklift to enter lanes for storing and retrieval, reducing the handling time and the risk of accident or damage to the racking structure. The Pallet Shuttle system offers a compact storage solution that reduces operating costs and improves performance in the supply chain. APC's semi-automated system stores and retrieves pallets from multiple deep racking using remote-controlled EAB RadioShuttle v6 Satellites with the ability to reach speeds of up to 1.1meter per second.Pallets move on a carrier shuttle that sits on rails installed in the racking system, thereby allowing easy back and forth retrievals. The user transmits a signal via a remote-control device for the shuttle to travel into the channel to store or retrieve pallets. While the Radioshuttle moves the pallet through the racking, the operator is free to do other work. Due to forklifts not having to enter the racking, costs associated with materials handling equipment are also minimised.
To ensure the racking was level, our in-house engineering team surveyed the site to attain the correct data to offset the posts in areas where the flooring was not level. A comprehensive chart detailing all level variations was produced so we could accurately offset each post. Some posts were offset using shims, designed to fill gaps of up to 30mm. However, most areas in the warehouse required a gap of more than 100mm to be filled. In these instances, grout was used to attain the correct levelling. The result is a level Satellite Racking System across the warehouse.
Result
The client was impressed with APC's ability to identify a high-density storage solution to maximise their warehouse space including the full height of the warehouse building. Our solution saves in space, time and costs associated with materials handling damage. By surveying the site and compiling the accurate date, our design team was able to ensure the racking was level across the entire warehouse floor.
Take a look at how Satellite Racking works.