Wheatstone LNG plant
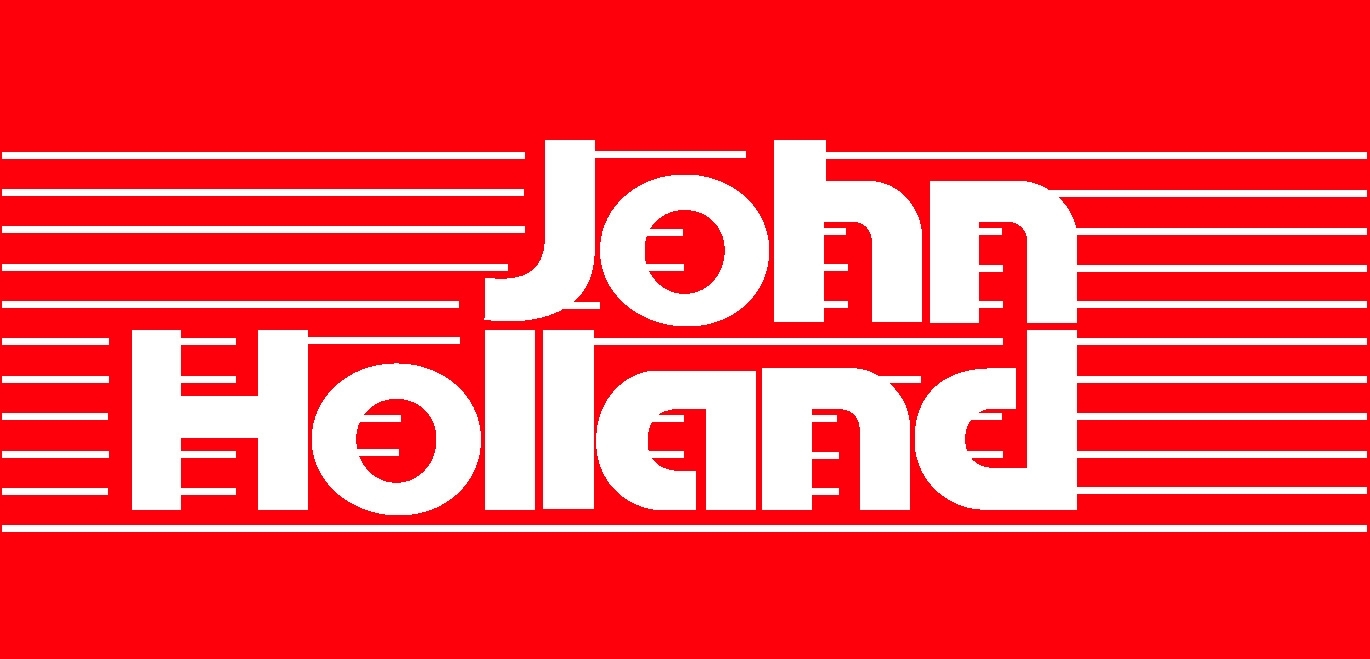
Client: John Holland
Location: Onslow, Western Australia
Wheatstone LNG is a $30m liquefied natural gas plant located in the Ashburton North Strategic Industrial Area, near Onslow, Western Australia. It is run and operated by Chevron Australia. John Holland were brought on as engineering contractors for the design and construction of the plant. They in turn engaged APC for the design, manufacture, supply and installation of an extensive, custom-built storage solution.
Briefing
John Holland required a contractor with in-house expertise to complete a project of Wheatstone's size, scope and complexity. Climate controlled and ambient raised storage areas were required to cover a combined surface area of 800m2. A highly customised, seismic-designed warehouse racking system with over 1500 pallet positions was also supplied. The structures were constructed from APC heavy duty racking and shelving and integrated with hot-dip galvanised steel floor grating (AS1657 compliant). Special finishes were applied to the racking structure during the manufacturing process to combat the aggressive environmental factors. Both super structures were integrated with goods hoists.
Challenge
Rather than deal with several suppliers, John Holland required a Design and Construct contractor to take on the project, that would include all design, supply, installation and project management of the racking systems; as well as the cladding, goods hoists, air conditioning, communications, electrical and lighting systems. The engineering, design, manufacturing, delivery and installation process needed to comply with Chevron’s stringent global standards, the Building Code of Australia and relevant Australian standards. There was a six month time frame from concept to commissioning so the process of design approval and logistics had to be executed swiftly. Because of the site’s remoteness and tight project milestone deliverables, the project demanded a fluid supply chain approach.
Solution
A combination of engineering software including Tekla, Spacegass and Strand7 was used to produce relevant calculations and generate modelling for the final design. Due to the ‘explosion proof’ rating of the building, APC engineers used seismic engineering criteria to design and develop the main structure. Galvanised APC Uni-shelving was required for small and sensitive parts storage for 22,000 SKU’S and integrated into the main structure along with two goods lifts. APC assigned a dedicated project management team to collaborate with the site’s three client project management teams representing John Holland, Chevron and Bechtel. Consequently, multiple channels of information and design input needed to be assessed to determine the final design and implementation. Detailed building and services clash checks were also undertaken to ensure total integration of the design and construction process.
Result
APC’s project management module, with its foundation in ISO accreditation, ensured we exceeded requirements, met all compliances and delivered an intelligent and robust design on time and on budget. As a turnkey design and construct project, APC were able to adapt our expertise to adjust to variable planning phase demands and use proven project realisation principles for the successful delivery of the project.